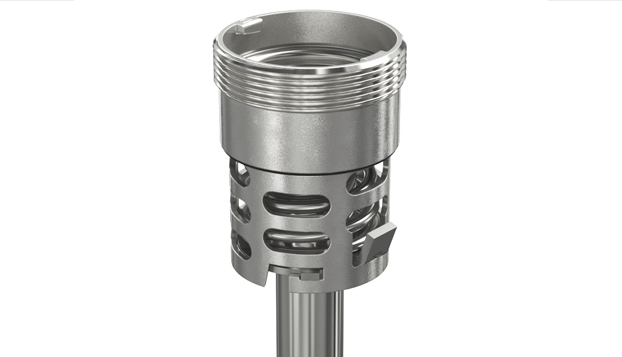
Fittings / Spear
Everything You Need to Know About Keg Fittings
Keg fittings (spears) are special connectors and valves used to connect beer kegs to tapping systems. They allow for the safe and hygienic dispensing of beer from the keg. There are different types of fittings that vary depending on the region and type of beer. It is crucial to choose the correct keg fittings for each keg to ensure that the dispensing process is efficient and hygienic. Brewery staff should familiarize themselves with the various types of keg fittings to make the best choice for their brewery. The most common types of fittings are:
FITTING SYSTEMS
A-System Fitting (Flat Fitting or Key Keg Fitting): Commonly used in Europe, the A-System is a flat design slide coupler with a round flange. The fitting is made of high-quality nickel-plated brass and a stainless steel probe. All parts that come into contact with beer are stainless steel to avoid any metallic taste.
G-System Fitting (Grundy): Used primarily in the UK, the G-System is similar in structure to the A-System but differs in its triangular housing design instead of a round one. It is applied and then twisted into place.
S-System Fitting (European Sankey): This system is common in Europe and is similar to the American Sankey fitting. It can be recognized by its basket-like housing. The fittings are made of stainless steel for maximum stability and hygiene and feature a dual valve function for fast filling.
M-System Fitting (Combo Fitting): Less commonly used and designed for certain beers and regions, M-System fittings combine features of flat and basket fittings. Internally, they resemble basket fittings, while their housing is designed after flat fittings for their hygienic benefits. From the top, they appear as flat with a "bulb" in the center.
A, M, and G fittings are more hygienic than the S-System because dirt and beer residue can accumulate more easily in the S-System’s basket.
Special tools are required for installing and maintaining fittings, such as decompression keys, disassembly tools, and assembly guns.
CO2 gasket color coding helps with manual or camera-based separation of kegs for routine maintenance.
Stainless Steel Fittings - Threaded or Threadless?
Stainless steel fittings can come with or without threads, depending on brewery needs. Threaded fittings are generally easier to install and are advantageous in situations requiring disassembly for maintenance or adjustments. However, they also need careful sealing to avoid leaks. Threadless fittings offer a secure connection without the risk of human error.
An example is the RS-SOS, a basket fitting without threads. It is fixed in the keg with a safety ring, also called a snap ring or C-clip. Once installed, it can be identified from above by its notch and the safety ring.
These fittings ensure beer is dispensed from the keg without contamination and at the right pressure. They are a critical part of beer filling and dispensing systems.
Fitting Components and Related Aspects
In addition to the types mentioned, there are several other aspects and components related to keg fittings:Function and Structure:
- Head and Valve: The fitting consists of a head that is mounted on the top of the keg and a valve mechanism that releases the beer when pressure is applied.
- Seals: Rubber gaskets and O-rings are essential to prevent leaks and ensure a secure connection.
Cleaning and Maintenance:
- Regular cleaning is necessary to maintain hygiene and beer quality.
- Maintaining and replacing worn-out parts, such as seals, is vital for the longevity of the fittings.
Materials:
- Fittings are often made of stainless steel due to its durability and ease of cleaning.
- Plastic components may be used in some parts but must be food-grade.
Compatibility and Standards:
- Different breweries and regions use specific fitting types, so compatibility with the tapping system must be considered.
- There are standards regulating the manufacture and use of fittings to ensure safety and quality.
Pressure Regulation:
- Fittings are often part of a system that regulates the pressure in the keg to ensure a steady and controlled flow of beer.
- CO2 or nitrogen tanks are used to create the necessary pressure.
Specialized Fittings:
- There are special fittings for different types of beverages, such as craft beers, which may have unique pressure and temperature requirements.
Connection to Tapping Systems:
- The fitting allows connection to hoses that transport the beer to the tapping system.
- Quick-connectors and hose couplers are often part of the system to ensure easy handling and flexibility.
Use Cases:
- Hospitality Industry: Fittings are used intensively to ensure efficient and hygienic beer dispensing.
- Events and Festivals: Mobile dispensing systems used at large events require reliable fittings.
- Breweries and Filling Lines: Fittings are crucial in the beer filling and storage process in breweries.
Technological Developments:
- Automated Cleaning Systems: Modern systems integrate automated cleaning cycles for fittings and tapping systems.
- Sensors and Monitoring: Sensors can be integrated to monitor the keg's fill level and pressure, allowing more precise control.
- Material Innovations: New materials and coatings can enhance the durability and hygiene of fittings.
Safety Considerations:
- Pressure Safety: Fittings must withstand high pressure to prevent leaks and accidents.
- Food Safety: All materials used must be food-grade and resistant to beer and cleaning agents.
Training and Certification:
- Staff Training: Proper handling and maintenance of fittings require trained personnel to ensure quality and hygiene.
- Certifications: Training and certification by breweries or technical service providers can increase staff competency.
Environmental Considerations:
- Sustainability: Reusable and durable fittings help reduce waste.
- Recycling: At the end of their life cycle, fitting materials should be recyclable.
Ergonomics and Design:
- User-Friendliness: Fittings should be designed to be easy to handle and maintain.
- Modular Systems: Modular components make it easier to replace parts without dismantling the entire system.
Brands and Manufacturers:
- There are numerous manufacturers and brands producing fittings, such as Micro Matic, DSI, and Cornelius. Each manufacturer may have specific designs and systems compatible with certain kegs and tapping systems.
Innovation and Research:
- Continuous Development: The industry is constantly searching for new technologies and materials to improve the efficiency, safety, and user-friendliness of fittings.
- Custom Solutions: Custom designs and adaptations can meet the specific needs of breweries or event organizers.
Historical Background:
- Development of Technology: Keg fitting technology has evolved over decades, from simple hand pumps to modern, precise systems.
- Impact of Industrialization: The standardization of fitting types and sizes became necessary with industrialization and the mass consumption of beer.
Regional Differences and Standards:
- Europe vs. North America: Different countries have their own standards and preferred fittings, affecting international collaboration and exports.
- DIN and ISO Standards: In Europe, many fittings are standardized according to DIN (German Industry Standard) and ISO (International Organization for Standardization) standards.
Tapping Systems and Accessories:
- Complete Systems: Fittings are part of complex systems that include CO2 tanks, pressure regulators, hoses, and taps.
- Temperature Control: Cooling systems are often integrated to keep the beer at the optimal temperature.
Consumer Trends and Market Demands:
- Craft Beer Movement: The demand for specialty beers has led to a diversification of fittings to accommodate smaller and differently shaped kegs.
- Sustainability: Environmentally conscious consumers demand sustainable practices, including reusable and recyclable fittings.
Logistics and Transport:
- Transport Conditions: Kegs must be transported securely, and fittings help prevent leaks and contamination.
- Traceability: Modern fittings may be equipped with RFID chips to track the location and usage of kegs.
Safety Regulations:
- Occupational Safety: Fittings should be designed to minimize the risk of injury, such as sharp edges or difficult-to-operate mechanisms.
- Regulatory Bodies: Institutions like the FDA (Food and Drug Administration) in the USA or the BfR (Federal Institute for Risk Assessment) in Germany monitor standards and safety regulations.
Innovative Technologies:
- Digital Monitoring: IoT (Internet of Things) technologies enable digital monitoring and control of fittings, such as real-time pressure and temperature monitoring.
- Self-Cleaning Systems: New materials and designs can support the self-cleaning of fittings, reducing maintenance efforts.
Custom Solutions:
- Tailored Solutions: Manufacturers often offer custom solutions to meet the specific needs of breweries or catering establishments.
- Branding and Marketing: Fittings and keg caps can be branded to display the brewery’s logo, which enhances marketing efforts.